Someone school me on aftermarket rims
#1
Senior Member
Thread Starter
Join Date: Sep 2011
Location: Bay Area, CA
Posts: 347
Likes: 0
Received 0 Likes
on
0 Posts
2006 E55 AMG
Someone school me on aftermarket rims
I'm thinking about getting some rims for my E55. Initially I wanted some black ones but now I'm seeing this look everywhere and kind of want to get something a little more elegant, so I'm thinking a brushed silver wheel.
My question is, whats the real difference between most rims? For example 3 piece vs forged wheels. I hear forged are usually lighter, but 3 piece may be better if only one part of the rim is damaged, you don't have to replace the whole thing?
Also, I don't want to get stuck with a brand thats associated with ghetto rims. Actually most brands are, but is there really a difference in quality, or is it just style?
Maybe something like this:

Or a darker brushed finish like this:
My question is, whats the real difference between most rims? For example 3 piece vs forged wheels. I hear forged are usually lighter, but 3 piece may be better if only one part of the rim is damaged, you don't have to replace the whole thing?
Also, I don't want to get stuck with a brand thats associated with ghetto rims. Actually most brands are, but is there really a difference in quality, or is it just style?
Maybe something like this:

Or a darker brushed finish like this:

Last edited by CityOfAngels; 12-19-2011 at 09:01 PM.
#2
MBWorld Fanatic!
i dont know what your style is but i just came across these and think they are pretty amazing... tempting me bad
http://www.ebay.com/itm/20-BLACK-SPO...ht_2574wt_1918
http://www.ebay.com/itm/20-BLACK-SPO...ht_2574wt_1918
#3
Super Member
Join Date: Apr 2009
Location: Houston, Tx
Posts: 619
Likes: 0
Received 0 Likes
on
0 Posts
'07 e63 AMG, '06 e320 CDI, '07 ML350 4Matic, '18 Gls450, '12 cls550
3 piece wheels will be more expensive, if your on a budget.
Forged wheels will be lighter
Brands that wouldn't be associated to ghetto lol: Mandrus, HRE, BBS, brabus, Vossen
There's ALOT more if you look into it
As for me I had Mandrus Milleniums back when I had my w209
Forged wheels will be lighter
Brands that wouldn't be associated to ghetto lol: Mandrus, HRE, BBS, brabus, Vossen
There's ALOT more if you look into it
As for me I had Mandrus Milleniums back when I had my w209
#4
Super Member
Join Date: Apr 2009
Location: Houston, Tx
Posts: 619
Likes: 0
Received 0 Likes
on
0 Posts
'07 e63 AMG, '06 e320 CDI, '07 ML350 4Matic, '18 Gls450, '12 cls550
i dont know what your style is but i just came across these and think they are pretty amazing... tempting me bad
http://www.ebay.com/itm/20-BLACK-SPO...ht_2574wt_1918
http://www.ebay.com/itm/20-BLACK-SPO...ht_2574wt_1918
+1 those look real nice!
#6
Super Member
Join Date: Apr 2009
Location: Houston, Tx
Posts: 619
Likes: 0
Received 0 Likes
on
0 Posts
'07 e63 AMG, '06 e320 CDI, '07 ML350 4Matic, '18 Gls450, '12 cls550
#7
Super Member
Join Date: Jan 2004
Location: Del Mar, CA
Posts: 939
Likes: 0
Received 4 Likes
on
4 Posts
2003 CL600 2005 745Li
18" - 19 / 21 LBS
19" - 21 / 23 LBS
TSW - Interlagos (kind of a Black Series look) and Nurburgring
http://www.tsw.com/alloy_wheels_interlagos.php
http://www.tsw.com/alloy_wheels_nurburgring.php
You can get 19" $1k and 18" can be had for $800
Of the 2 sets of their Rotatory Forged line I like these, and it would be VERY hard to beat their price on such a light weight wheel.






Trending Topics
#9
Here's an article from Carlos - Lead engineer at MORR. Consider this a wheel bible 
We offer forged wheels from MORR, COR Forged, D2 Forged, Iforged and DPE(1 piece and 3 piece), low pressure cast wheels from AvantGarde and Vossen and flow formed wheels from Forgestar.
Link:
http://www.campionishop.com/category...x?cid=3&clev=0
One of the most controversial areas of wheel manufacturing is the manufacturer testing policies or testing guidelines. In this article we’ll cover the major worldwide testing standards, procedures, requirements, specifications, cost and certifications. Whether testing and certification is important I’ll leave it up to you to draw that conclusion after reading this article. Source of this information is my direct experience of nearly a decade in the automotive industry, information directly from the testing council’s official websites, Official documents, Press releases, Wikipedia and other sources.
There are the major test standards:
Background:
JWL is the quality testing standard for Japan. The Japan Light Alloy Wheel (JWL) standard is a set of performance requirements for alloy wheels overseen by the Japan Light Allow Wheel Testing Council (JWTC) in Japan. This set of standards is required for all wheels in Japan and is set by the Ministry of Land, Infrastructure, Transport and Tourism (MLIT) of this country. This ministry is part of the Japanese government and it’s responsible for the majority of Japanese laws and orders, only second to the department of defense. This standard was developed by the Japanese government to ensure the safety of automobile alloy wheels and truck. JWL Testing and certification is mandatory in Japan.
Japan Light Allow Wheel Testing Council is a cooperation between the MLIT , Japan Aluminum Association (JAA), Nippon Auto Parts Aftermarket Committee (JAWA) and Japan Vehicle Inspection Association (VIA).
Testing Requirements:
The JWL testing standards require the following tests to be performed on all passenger alloy wheels:
- Dynamic Cornering Fatigue Test
- Dynamic Radial Fatigue Test
- Impact Test
Certification and Marks:
The JWL is a self-certified test by the wheel manufacturer. Manufacturers register and certify their testing equipment with the JWTC and are then able to certify their own wheels to JWL standards and cast or forge the JWL mark onto the wheel. Once this is done the wheel is considered JWL Certified.

VIA has established a set of parameter to independently test and register the wheels to JWL or JWL-T standards. Only once VIA has tested and certified the wheels to JWL standards it can bear the VIA mark as well as the JWL mark and it’s then considered JWL Certified and VIA Registered.
It is very important to distinguish the difference between the two.


Cost:
Total cost to conduct a JWL testing and VIA certification is approximately ¥;99,650 Yen or $1,295.00 US Dollars per style and can be done simultaneously to a range of PCD or offsets. It requires approx. 3 – 4 samples wheels.
Background:
TUV (Technischer Überwachungs-Verein) is the quality testing standard for Germany. It translates to Technical Inspection Association. Every german-registered vehicle must have a certificate from TUV in order to be operated in public roads.
Testing Requirements:
The TUV testing standards require the following tests to be performed on all passenger alloy wheels:
- Dynamic Cornering Fatigue Test – Short
200,000 Cycles at 75% Max Load.
- Dynamic Cornering Fatigue Test – Long
1,800,000 Cycles at 50% Max Load.
- Dynamic Radial Fatigue Test
2000km at 2.5 Wheel Load.
- Impact Test at Valve Hole
- Impact Test in between Spokes.
- Alternating Corrosion Test
- Corrosion Test
- Material Testing
- Mounting Test
Certification and Marks:
Once a wheel has been tested and approved by the TUV, a TUV certificate is issued and a black/color copy can be included with every wheel purchase. The TUV logo can be display in the product literature, product packaging and company website.
TUV verification cannot be confused with TUV certification. TUV verification implies that the company follows a set of quality/manufacturing guidelines approved and certified by TUV. TUV certification means that a wheel has been independently tested and certified to a set of performance standards set forth by TUV.

Cost:
Total cost to conduct a TUV testing and certification is approximately €4,950 Euro or $6,800.00 US Dollars per style, per fitment, per vehicle. This fee excludes a KBA approval charge of US$750 and a Application Test Report fee of US$500. It requires over 10 sample wheels.
The manufacturer and every facility where work to the wheel is done must be ISO: 9001 certified. Cost to obtain ISO accreditation is in excess of $10,000 US Dollars per facility and must be done on a yearly basis.
SAE stands for Society of Automotive Engineers. From the SEMA website: A few years ago, SEMA and its Wheel & Tire Council (WTC) worked with the Society of Automotive Engineers (SAE) to develop an industry testing practice for aftermarket wheels. SAE J2530 (Aftermarket Wheels Performance Requirements and Testing Procedures) outlines performance and sampling guidelines, testing procedures and marking requirements for aftermarket wheels used on cars, light trucks and multipurpose vehicles. The document identifies three main areas of testing, including cornering and radial fatigue and impact strength. A manufacturer can purchase the J2530 specifications from SAE and test at its own internal lab or at any testing facility of its choosing, so long as that facility maintains the necessary equipment to perform the tests.
Testing Requirements:
The SAE testing standards require the following tests to be performed on all passenger alloy wheels, based on a Sample size of 2:
- Dynamic Cornering Fatigue Test
475,000 Cycles @ 1.35 Factor load
- Dynamic Radial Fatigue Test
1,850,000 Cycles @ 2.0 Factor Load
- Impact Test at 13°
Certification and Marks:
Wheels that conform to the SAE J2530 Standard must be marked with:
- Wheel Manufacturer’s name
- Date of Manufacture
- Part number
- Country of Manufacture
- Rim Size
- Wheel load Rating
- DOT Symbol
- SAE J2530 must be casted in, stamped on or label on wheels that conform to this standard.

Cost:
Total cost to conduct a SAE J2530 certification is approximately $1,295.00 US Dollars per style, per fitment. It requires approx. 5 samples wheels.

We offer forged wheels from MORR, COR Forged, D2 Forged, Iforged and DPE(1 piece and 3 piece), low pressure cast wheels from AvantGarde and Vossen and flow formed wheels from Forgestar.
Link:
http://www.campionishop.com/category...x?cid=3&clev=0
Lately, I have seen a lot of people asking questions about wheels, their strength, weight, manufacturing method, which wheels are good, what to buy, etc and I’ve seen some very good responses but I have also seen some misleading opinions so I decided to write this series of articles to make sure you know everything you need to know about wheels.
This information comes from over 5 years of experience in the automotive wheel industry. I’m an Industrial Engineer with a minor in Mechanical Design, I own two wheel companies, have dealt with every aftermarket forged wheel manufacturer in the world, have designed, engineered and manufactured very strong and light wheels in both cast and forged variants and have very close relationships with some of the leaders of the wheels industry in the USA including members of the SAE Aftermarket Wheel Committee and the SEMA Wheel Industry Council.
Here is the first article. Hope you like it and could use it to form accurate opinions about your future wheel purchase and can properly and accurately assist others.
Alloy wheels, or most commonly known as “rims” are automobile wheels that are manufactured from aluminum or magnesium alloy metals. They are called alloy wheels since they are not manufactured from pure aluminum or magnesium but using alloys (mix of metals) usually 6000-Series for high end aluminum wheels which contains less than 1% Si and about 1% magnesium.
6060-T6 Aluminum is very good because of its properties. It is very ductile, durable and lightweight, making it very good among wheel manufacturers. The “T6” comes from a Heat Treatment technique called precipitation hardening and an artificially aging process to alter the properties of the alloy
Automotive wheels can be manufactured using several process. Setian (DTMRack.com) and crimsone90 made very good articles referring these methods. This articles can be found here (http://www.m3post.com/forums/showthread.php?t=357430) and here: (http://www.e90post.com/forums/showthread.php?t=295274).
Casting
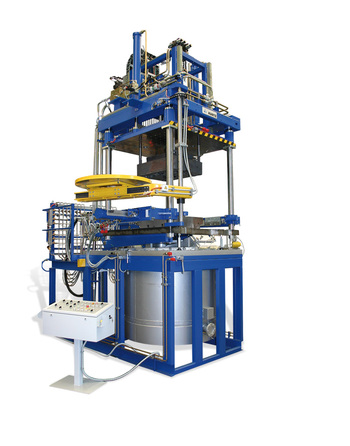
Most of you are familiar with this process.
By definition, “Casting is a manufacturing process by which a liquid material is usually poured into a mold, which contains a hollow cavity of the desired shape, and then allowed to solidify.” There are two main techniques to cast aluminum wheels, gravity casting and low-pressure casting.
Gravity casting is a method of manufacturing a cast wheel of an specific metal alloy, typically aluminum, although Magnesium is also used, which involves supplying molten metal to a mould cavity via a feeder through a running system where the molten metal entry point is located above the top of the mould cavity. In this manufacturing process all the metal entering the mould is subject to turbulence. This turbulence can cause severe defects such as oxide inclusions and entrapped gas porosity and in some cases mould erosion and hotspots.
Low-pressure casting in the other hand takes care of the disadvantages of Gravity casting by filling the mould by injecting molten metal at about 25psi through an in-gate just below the top of the mould cavity from a source under the mould through a method which allows complete filling of the mould. The force of gravity acts against the upward flow of the metal and eliminates the possible turbulence caused by the falling liquid metal. The molten metal is stored in a pressured container and by increasing the pressure metal is then forced into the mould.
In low-pressure casting the method in which the metal is forced into the mould is the main difference/advantage over gravity casting and is absolutely controlled. As explained above it results in a low turbulence or turbulence-free mould filling with little to no corrosion.
The molten metal in the furnace is in a closed container under protected atmosphere. Because of this the metal absorbs less hydrogen and any other impurities as well as the oxide formation being greatly reduced. As opposed to gravity casting, the metal surface is not interrupted constantly since it is been forced from under the metal surface. What you get is a very clean quality metal.
Basically low-pressure casting uses positive pressure to move molten metal into the mold quickly thus resulting in a finished product with an Aluminum that is denser than Gravity cast.
The advantages of low pressure die casting process are several:
- higher yield achievable
- reduction of machining costs
- excellent control of process parameters
- good metallurgical quality
- leads to an optimal use of the aluminum
- excellent mechanical and technological properties of the castings.
Forging:

Out of the three, Forging is the manufacturing process that creates the lightest metals. There are several ways to forge alloy wheels, but the most common is press forging.
By definition “Forging is the shaping of metal using localized compressive forces. It is to form or to make by heating and pressing.”
The forging process uses immense amounts of compressive force to shape the metal. During this process a wheel blank is placed between two shaped plates and the press slowly shapes the wheel using continuous forces. During the process the internal grain is deformed and rearranged to the shape of the part. This deformation due to compressive force improves the strength uniformly throughout the entire structure of the wheel. Press Forging allows closer tolerances as well. The wheel is typically heated to about 400-Farenheit. The forging process typically uses anything between 4,000 to 10,000 tons of pressure, 6000 being the most common, and reaches up to 16,000 tons to produce forged magnesium wheels. Heat treatment and artificial aging can further improve the wheel mechanical properties.
It is important to understand that forging does not compress the metal. Forging alters the grain structure of the metal and makes it stronger. For example, a 19” aluminum wheel blank that weights 30lbs will still weight 30lbs after the forging process. The major difference is that after the forging process, the 30lbs forged aluminum wheel blank will be much stronger. Since the aluminum is stronger it allows the engineers to manufacture a lighter wheel by removing excess aluminum.
To make it easier to understand, imagine a structure that requires a beam with a diameter of 5-inches. If we manufacture that beam out of forged aluminum, since the mechanical properties have been improved, the beam diameter could now be reduced to around 2-3” in diameter helping to make the structure lighter. You could do the same and keep the diameter of the beam at 5-inches if your purpose is to make it stronger.
In other words, Forging does not make the metal lighter, it makes it stronger. Forged wheels are also formed via flow-forming which is explained below.
Flow-Forming:

Flow Forming is a precision metal forming. It is commonly known as a forming technique. It is the newest player and is only available by a limited number of manufacturer.
By definition: “Flow Forming is an incremental metal forming technique in which a disk or tube of metal is formed over a mandrel by one or more rollers using tremendous pressure.”
In other words, a disk, or in this case an aluminum wheel blank, is placed between two rollers and the wheel spins while the two rollers form the barrel at high pressures and extends the barrel of the wheel to the desired length. This deformation arranges the grain structure of the metal in the direction of the rotation of the wheel. The blank is typically made using metal casting. This process helps reduce barrel thickness. The blank barrel is usually around 4.0-9.0-inches wide and is extended to 7.0”-11.0-inches depending on the application. Although the piece is cold formed, during the forming process, due to friction, the wheel blank is heated to around 400-Farenheit. Because of the high pressure and high temperature the metal mechanical properties are changed. The mechanical properties of the metal became very similar, if not the same, to that of a forged wheel. No material is lost during the forming process, resulting in less aluminum used to create the finished wheel.
Flow Forming in essence forges the wheel barrel by spinning and forming. Forming can be done hot, warm or cold and is accomplished on mechanical or hydraulic press, or on special forming equipment. Heat treatment and artificial aging can further improve the wheel mechanical properties. Flow forming process can be a cost-effective alternative to conventional press forging.
Because of its properties flow forming is also known as liquid forging.
Please let me know if you have any questions regarding this and I`ll try to reply them as soon as possible.
This information comes from over 5 years of experience in the automotive wheel industry. I’m an Industrial Engineer with a minor in Mechanical Design, I own two wheel companies, have dealt with every aftermarket forged wheel manufacturer in the world, have designed, engineered and manufactured very strong and light wheels in both cast and forged variants and have very close relationships with some of the leaders of the wheels industry in the USA including members of the SAE Aftermarket Wheel Committee and the SEMA Wheel Industry Council.
Article 1
Here is the first article. Hope you like it and could use it to form accurate opinions about your future wheel purchase and can properly and accurately assist others.
What are Alloy Wheels?
Alloy wheels, or most commonly known as “rims” are automobile wheels that are manufactured from aluminum or magnesium alloy metals. They are called alloy wheels since they are not manufactured from pure aluminum or magnesium but using alloys (mix of metals) usually 6000-Series for high end aluminum wheels which contains less than 1% Si and about 1% magnesium.
6060-T6 Aluminum is very good because of its properties. It is very ductile, durable and lightweight, making it very good among wheel manufacturers. The “T6” comes from a Heat Treatment technique called precipitation hardening and an artificially aging process to alter the properties of the alloy
Manufacturing:
Automotive wheels can be manufactured using several process. Setian (DTMRack.com) and crimsone90 made very good articles referring these methods. This articles can be found here (http://www.m3post.com/forums/showthread.php?t=357430) and here: (http://www.e90post.com/forums/showthread.php?t=295274).
Casting
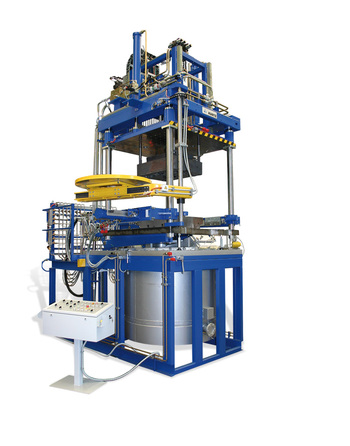
Most of you are familiar with this process.
By definition, “Casting is a manufacturing process by which a liquid material is usually poured into a mold, which contains a hollow cavity of the desired shape, and then allowed to solidify.” There are two main techniques to cast aluminum wheels, gravity casting and low-pressure casting.
Gravity casting is a method of manufacturing a cast wheel of an specific metal alloy, typically aluminum, although Magnesium is also used, which involves supplying molten metal to a mould cavity via a feeder through a running system where the molten metal entry point is located above the top of the mould cavity. In this manufacturing process all the metal entering the mould is subject to turbulence. This turbulence can cause severe defects such as oxide inclusions and entrapped gas porosity and in some cases mould erosion and hotspots.
Low-pressure casting in the other hand takes care of the disadvantages of Gravity casting by filling the mould by injecting molten metal at about 25psi through an in-gate just below the top of the mould cavity from a source under the mould through a method which allows complete filling of the mould. The force of gravity acts against the upward flow of the metal and eliminates the possible turbulence caused by the falling liquid metal. The molten metal is stored in a pressured container and by increasing the pressure metal is then forced into the mould.
In low-pressure casting the method in which the metal is forced into the mould is the main difference/advantage over gravity casting and is absolutely controlled. As explained above it results in a low turbulence or turbulence-free mould filling with little to no corrosion.
The molten metal in the furnace is in a closed container under protected atmosphere. Because of this the metal absorbs less hydrogen and any other impurities as well as the oxide formation being greatly reduced. As opposed to gravity casting, the metal surface is not interrupted constantly since it is been forced from under the metal surface. What you get is a very clean quality metal.
Basically low-pressure casting uses positive pressure to move molten metal into the mold quickly thus resulting in a finished product with an Aluminum that is denser than Gravity cast.
The advantages of low pressure die casting process are several:
- higher yield achievable
- reduction of machining costs
- excellent control of process parameters
- good metallurgical quality
- leads to an optimal use of the aluminum
- excellent mechanical and technological properties of the castings.
Forging:

Out of the three, Forging is the manufacturing process that creates the lightest metals. There are several ways to forge alloy wheels, but the most common is press forging.
By definition “Forging is the shaping of metal using localized compressive forces. It is to form or to make by heating and pressing.”
The forging process uses immense amounts of compressive force to shape the metal. During this process a wheel blank is placed between two shaped plates and the press slowly shapes the wheel using continuous forces. During the process the internal grain is deformed and rearranged to the shape of the part. This deformation due to compressive force improves the strength uniformly throughout the entire structure of the wheel. Press Forging allows closer tolerances as well. The wheel is typically heated to about 400-Farenheit. The forging process typically uses anything between 4,000 to 10,000 tons of pressure, 6000 being the most common, and reaches up to 16,000 tons to produce forged magnesium wheels. Heat treatment and artificial aging can further improve the wheel mechanical properties.
It is important to understand that forging does not compress the metal. Forging alters the grain structure of the metal and makes it stronger. For example, a 19” aluminum wheel blank that weights 30lbs will still weight 30lbs after the forging process. The major difference is that after the forging process, the 30lbs forged aluminum wheel blank will be much stronger. Since the aluminum is stronger it allows the engineers to manufacture a lighter wheel by removing excess aluminum.
To make it easier to understand, imagine a structure that requires a beam with a diameter of 5-inches. If we manufacture that beam out of forged aluminum, since the mechanical properties have been improved, the beam diameter could now be reduced to around 2-3” in diameter helping to make the structure lighter. You could do the same and keep the diameter of the beam at 5-inches if your purpose is to make it stronger.
In other words, Forging does not make the metal lighter, it makes it stronger. Forged wheels are also formed via flow-forming which is explained below.
Flow-Forming:

Flow Forming is a precision metal forming. It is commonly known as a forming technique. It is the newest player and is only available by a limited number of manufacturer.
By definition: “Flow Forming is an incremental metal forming technique in which a disk or tube of metal is formed over a mandrel by one or more rollers using tremendous pressure.”
In other words, a disk, or in this case an aluminum wheel blank, is placed between two rollers and the wheel spins while the two rollers form the barrel at high pressures and extends the barrel of the wheel to the desired length. This deformation arranges the grain structure of the metal in the direction of the rotation of the wheel. The blank is typically made using metal casting. This process helps reduce barrel thickness. The blank barrel is usually around 4.0-9.0-inches wide and is extended to 7.0”-11.0-inches depending on the application. Although the piece is cold formed, during the forming process, due to friction, the wheel blank is heated to around 400-Farenheit. Because of the high pressure and high temperature the metal mechanical properties are changed. The mechanical properties of the metal became very similar, if not the same, to that of a forged wheel. No material is lost during the forming process, resulting in less aluminum used to create the finished wheel.
Flow Forming in essence forges the wheel barrel by spinning and forming. Forming can be done hot, warm or cold and is accomplished on mechanical or hydraulic press, or on special forming equipment. Heat treatment and artificial aging can further improve the wheel mechanical properties. Flow forming process can be a cost-effective alternative to conventional press forging.
Because of its properties flow forming is also known as liquid forging.
Please let me know if you have any questions regarding this and I`ll try to reply them as soon as possible.
Article 2 - Design and & Engineering
This is my favorite area. Engineering is the most important part of the wheel developing process and is where a lot of wheel manufacturers fail. I’ll cover only some of the key factors under the design and engineering stage.
The weight and strength ratio of aluminum wheels is key when developing performance wheels. As explained above, aluminum does not become lighter through forging or forming. It only becomes stronger. Since it’s stronger, we can use LESS material to achieve the same level of strength. This is very important to understand.
For the purposes of explaining this, let’s assume we are designing our own wheel. We’ll call this wheel, the “M92”. This wheel will be 19 x 8.5” in size. We’ll assume we are designing this wheel and manufacturing in all three manufacturing methods: casting, forging and flow-forming. Please refer to the chart below:

As you can see, the same wheel design manufactured in the all various manufacturing processes will require the same weight (amount) of aluminum and therefore will have the same weight BUT different strength expressed as load ratings (explained below). In other words, since the design is the same, it’ll required the same amount of material to make it, however, since the mechanical properties of cast, forged or flow-formed aluminum are different the the strength level (load rating) will be different with cast being the heaviest, and forging leading in weight and forming coming in as close second. Please keep in mind different aluminum materials have different density so the weight might be slightly different.
Load Rating is the required load the wheels are capable of withstanding. Every organization has their recommended load ratings per application for which they test against. This might be done for safety reasons. For most BMWs this number is around 650kg – 730kg.The load rating requirements are determined by taking the vehicle's heaviest gross axle weight rating (GAWR) and diving that by 2. This number might be significantly lower than the recommended load rating established by international wheel quality standards.
Now, let’s assume that we are interested in having our M92 wheel rated at exactly 660kg per corner. Please refer to the chart below:

As you can see, since we are interested in achieving no more and no less than a load rating of 660kg per corner, via casting we’ll need to increase the weight of the wheel (add material) in order to achieve our desired load rating bringing the final weight to 26.2lbs. For Forming and Forging, since the aluminum is stronger than casting and the required load rating is LOWER than what our wheel is capable of holding at the current weight of 25.0lbs, then we are able to remove material from the wheel to achieve our required load rating and at the same time lose weight. In this case we are able reduce the weight to 23.6lbs and 22.8lbs accordingly, to achieve a load rating of 660kg.
Please note that “adding” and “removing” material can only be done during the design process. It cannot be done AFTER the wheel has already been made.
In conclusion, forged/formed wheels are not stronger than cast wheels. If rated at the same load, they will be lighter and equally strong. This is assuming they are all engineered equally.
I am a firm supporter of manufacturers that make wheels “model-specific”. Fitment on a vehicle is very important and can drastically change the dynamics of your car. Here we’ll discuss “model-specific” wheels vs “custom” wheels.
#1 – Load Ratings and Weight Reduction
Every vehicle requires its own specific offset, width, bolt pattern, fender, strut and brake clearance, back spacing, etc.
For example, lets say your jacket size is a 42L. Making a “Custom” wheel is like buying a 44R and “customizing it” in order to make it fit. It’ll never fit right and the quality won’t be the same. It is always better to buy a jacket that is already 42L!
The same goes with wheels. In order to built “custom” wheels, manufacturers take a blank and machine the back pad as much as they need to -sometimes up to 30mm --, require you to run spacers if the fitment is more aggressive, and provide centering rings in order to make it fit. It has gone to the extreme that not even your OEM centercaps and bolt lugs fit! What is custom about that?
A cast wheel should not be machine more than 3-5mm IF NECESSARY. A Forged wheel I wouldn’t shave more than 10mm of the back pad. This can SEVERELY deteriorate the integrity of the wheel! Removing material from the back pad can be a disaster. Adjusting offsets by milling several millimeters of the back pad is not the proper way to do it. This safety hazard is more present with cast wheel, but even with forged wheels there is a margin you cannot exceed. This is a potential safety hazard and could result in a complete wheel failure. The consequences of exceeding these limits are balancing issues, excessive run out, weaker structure and severe vibrations at high speed.
Using the same blanks across platforms (Same blanks for different brands) can limit your design due to brake clearances and force you to use under rated wheels (weak) or over rated wheels (heavy) for your vehicle.
Let’s use our M92 wheel as an example. Let’s say we make this wheel as a “generic blank” and then we would like to customize it for a Porsche.

In this case, since the wheel is being “custom made” for a Porsche application, requiring a lower load rating, and the blank used is a generic blank then the weight stays the same since you can no longer remove weight since the wheel is already made. Right now you are mounting a wheel on your vehicle that weights a few pounds more than what it should. You’ll also be required to use centering rings since the center bore is larger than the Porsche center bore.
Now let’s say you use a Porsche specific blank.

In this case since you are using a Brand-specific blank you have a lower weight (sine the actual load rating = required load rating) and the fitment will bolt on without any centering rings or spacers since is meant for the vehicle that is going into.
The other case is where the “custom” wheels is for an application that requires a higher load rating. In this case, your “custom” wheel will have a LOWER load rating than the recommended for your vehicle and could potentially be a safety hazard.
This is my favorite area. Engineering is the most important part of the wheel developing process and is where a lot of wheel manufacturers fail. I’ll cover only some of the key factors under the design and engineering stage.
Weight & Strength
The weight and strength ratio of aluminum wheels is key when developing performance wheels. As explained above, aluminum does not become lighter through forging or forming. It only becomes stronger. Since it’s stronger, we can use LESS material to achieve the same level of strength. This is very important to understand.
For the purposes of explaining this, let’s assume we are designing our own wheel. We’ll call this wheel, the “M92”. This wheel will be 19 x 8.5” in size. We’ll assume we are designing this wheel and manufacturing in all three manufacturing methods: casting, forging and flow-forming. Please refer to the chart below:

As you can see, the same wheel design manufactured in the all various manufacturing processes will require the same weight (amount) of aluminum and therefore will have the same weight BUT different strength expressed as load ratings (explained below). In other words, since the design is the same, it’ll required the same amount of material to make it, however, since the mechanical properties of cast, forged or flow-formed aluminum are different the the strength level (load rating) will be different with cast being the heaviest, and forging leading in weight and forming coming in as close second. Please keep in mind different aluminum materials have different density so the weight might be slightly different.
Load Rating is the required load the wheels are capable of withstanding. Every organization has their recommended load ratings per application for which they test against. This might be done for safety reasons. For most BMWs this number is around 650kg – 730kg.The load rating requirements are determined by taking the vehicle's heaviest gross axle weight rating (GAWR) and diving that by 2. This number might be significantly lower than the recommended load rating established by international wheel quality standards.
Now, let’s assume that we are interested in having our M92 wheel rated at exactly 660kg per corner. Please refer to the chart below:

As you can see, since we are interested in achieving no more and no less than a load rating of 660kg per corner, via casting we’ll need to increase the weight of the wheel (add material) in order to achieve our desired load rating bringing the final weight to 26.2lbs. For Forming and Forging, since the aluminum is stronger than casting and the required load rating is LOWER than what our wheel is capable of holding at the current weight of 25.0lbs, then we are able to remove material from the wheel to achieve our required load rating and at the same time lose weight. In this case we are able reduce the weight to 23.6lbs and 22.8lbs accordingly, to achieve a load rating of 660kg.
Please note that “adding” and “removing” material can only be done during the design process. It cannot be done AFTER the wheel has already been made.
In conclusion, forged/formed wheels are not stronger than cast wheels. If rated at the same load, they will be lighter and equally strong. This is assuming they are all engineered equally.
Fitment:
I am a firm supporter of manufacturers that make wheels “model-specific”. Fitment on a vehicle is very important and can drastically change the dynamics of your car. Here we’ll discuss “model-specific” wheels vs “custom” wheels.
#1 – Load Ratings and Weight Reduction
Every vehicle requires its own specific offset, width, bolt pattern, fender, strut and brake clearance, back spacing, etc.
For example, lets say your jacket size is a 42L. Making a “Custom” wheel is like buying a 44R and “customizing it” in order to make it fit. It’ll never fit right and the quality won’t be the same. It is always better to buy a jacket that is already 42L!
The same goes with wheels. In order to built “custom” wheels, manufacturers take a blank and machine the back pad as much as they need to -sometimes up to 30mm --, require you to run spacers if the fitment is more aggressive, and provide centering rings in order to make it fit. It has gone to the extreme that not even your OEM centercaps and bolt lugs fit! What is custom about that?
A cast wheel should not be machine more than 3-5mm IF NECESSARY. A Forged wheel I wouldn’t shave more than 10mm of the back pad. This can SEVERELY deteriorate the integrity of the wheel! Removing material from the back pad can be a disaster. Adjusting offsets by milling several millimeters of the back pad is not the proper way to do it. This safety hazard is more present with cast wheel, but even with forged wheels there is a margin you cannot exceed. This is a potential safety hazard and could result in a complete wheel failure. The consequences of exceeding these limits are balancing issues, excessive run out, weaker structure and severe vibrations at high speed.
Using the same blanks across platforms (Same blanks for different brands) can limit your design due to brake clearances and force you to use under rated wheels (weak) or over rated wheels (heavy) for your vehicle.
Let’s use our M92 wheel as an example. Let’s say we make this wheel as a “generic blank” and then we would like to customize it for a Porsche.

In this case, since the wheel is being “custom made” for a Porsche application, requiring a lower load rating, and the blank used is a generic blank then the weight stays the same since you can no longer remove weight since the wheel is already made. Right now you are mounting a wheel on your vehicle that weights a few pounds more than what it should. You’ll also be required to use centering rings since the center bore is larger than the Porsche center bore.
Now let’s say you use a Porsche specific blank.

In this case since you are using a Brand-specific blank you have a lower weight (sine the actual load rating = required load rating) and the fitment will bolt on without any centering rings or spacers since is meant for the vehicle that is going into.
The other case is where the “custom” wheels is for an application that requires a higher load rating. In this case, your “custom” wheel will have a LOWER load rating than the recommended for your vehicle and could potentially be a safety hazard.
Article 3
One of the most controversial areas of wheel manufacturing is the manufacturer testing policies or testing guidelines. In this article we’ll cover the major worldwide testing standards, procedures, requirements, specifications, cost and certifications. Whether testing and certification is important I’ll leave it up to you to draw that conclusion after reading this article. Source of this information is my direct experience of nearly a decade in the automotive industry, information directly from the testing council’s official websites, Official documents, Press releases, Wikipedia and other sources.
Testing and Certification
There are the major test standards:
JWL
Background:
JWL is the quality testing standard for Japan. The Japan Light Alloy Wheel (JWL) standard is a set of performance requirements for alloy wheels overseen by the Japan Light Allow Wheel Testing Council (JWTC) in Japan. This set of standards is required for all wheels in Japan and is set by the Ministry of Land, Infrastructure, Transport and Tourism (MLIT) of this country. This ministry is part of the Japanese government and it’s responsible for the majority of Japanese laws and orders, only second to the department of defense. This standard was developed by the Japanese government to ensure the safety of automobile alloy wheels and truck. JWL Testing and certification is mandatory in Japan.
Japan Light Allow Wheel Testing Council is a cooperation between the MLIT , Japan Aluminum Association (JAA), Nippon Auto Parts Aftermarket Committee (JAWA) and Japan Vehicle Inspection Association (VIA).
Testing Requirements:
The JWL testing standards require the following tests to be performed on all passenger alloy wheels:
- Dynamic Cornering Fatigue Test
- Dynamic Radial Fatigue Test
- Impact Test
Certification and Marks:
The JWL is a self-certified test by the wheel manufacturer. Manufacturers register and certify their testing equipment with the JWTC and are then able to certify their own wheels to JWL standards and cast or forge the JWL mark onto the wheel. Once this is done the wheel is considered JWL Certified.

VIA has established a set of parameter to independently test and register the wheels to JWL or JWL-T standards. Only once VIA has tested and certified the wheels to JWL standards it can bear the VIA mark as well as the JWL mark and it’s then considered JWL Certified and VIA Registered.
It is very important to distinguish the difference between the two.


Cost:
Total cost to conduct a JWL testing and VIA certification is approximately ¥;99,650 Yen or $1,295.00 US Dollars per style and can be done simultaneously to a range of PCD or offsets. It requires approx. 3 – 4 samples wheels.
TUV
Background:
TUV (Technischer Überwachungs-Verein) is the quality testing standard for Germany. It translates to Technical Inspection Association. Every german-registered vehicle must have a certificate from TUV in order to be operated in public roads.
Testing Requirements:
The TUV testing standards require the following tests to be performed on all passenger alloy wheels:
- Dynamic Cornering Fatigue Test – Short
200,000 Cycles at 75% Max Load.
- Dynamic Cornering Fatigue Test – Long
1,800,000 Cycles at 50% Max Load.
- Dynamic Radial Fatigue Test
2000km at 2.5 Wheel Load.
- Impact Test at Valve Hole
- Impact Test in between Spokes.
- Alternating Corrosion Test
- Corrosion Test
- Material Testing
- Mounting Test
Certification and Marks:
Once a wheel has been tested and approved by the TUV, a TUV certificate is issued and a black/color copy can be included with every wheel purchase. The TUV logo can be display in the product literature, product packaging and company website.
TUV verification cannot be confused with TUV certification. TUV verification implies that the company follows a set of quality/manufacturing guidelines approved and certified by TUV. TUV certification means that a wheel has been independently tested and certified to a set of performance standards set forth by TUV.

Cost:
Total cost to conduct a TUV testing and certification is approximately €4,950 Euro or $6,800.00 US Dollars per style, per fitment, per vehicle. This fee excludes a KBA approval charge of US$750 and a Application Test Report fee of US$500. It requires over 10 sample wheels.
The manufacturer and every facility where work to the wheel is done must be ISO: 9001 certified. Cost to obtain ISO accreditation is in excess of $10,000 US Dollars per facility and must be done on a yearly basis.
SAE
SAE stands for Society of Automotive Engineers. From the SEMA website: A few years ago, SEMA and its Wheel & Tire Council (WTC) worked with the Society of Automotive Engineers (SAE) to develop an industry testing practice for aftermarket wheels. SAE J2530 (Aftermarket Wheels Performance Requirements and Testing Procedures) outlines performance and sampling guidelines, testing procedures and marking requirements for aftermarket wheels used on cars, light trucks and multipurpose vehicles. The document identifies three main areas of testing, including cornering and radial fatigue and impact strength. A manufacturer can purchase the J2530 specifications from SAE and test at its own internal lab or at any testing facility of its choosing, so long as that facility maintains the necessary equipment to perform the tests.
Testing Requirements:
The SAE testing standards require the following tests to be performed on all passenger alloy wheels, based on a Sample size of 2:
- Dynamic Cornering Fatigue Test
475,000 Cycles @ 1.35 Factor load
- Dynamic Radial Fatigue Test
1,850,000 Cycles @ 2.0 Factor Load
- Impact Test at 13°
Certification and Marks:
Wheels that conform to the SAE J2530 Standard must be marked with:
- Wheel Manufacturer’s name
- Date of Manufacture
- Part number
- Country of Manufacture
- Rim Size
- Wheel load Rating
- DOT Symbol
- SAE J2530 must be casted in, stamped on or label on wheels that conform to this standard.

Cost:
Total cost to conduct a SAE J2530 certification is approximately $1,295.00 US Dollars per style, per fitment. It requires approx. 5 samples wheels.
The following users liked this post:
DuhStig (12-05-2021)
#12
Senior Member
www.1010tires.com/wheeloffsetcalculator.asp is useful if changing widths and diameter.
www.powerwheelspro.com supply some great replica rims and are high quality.
Be careful with replica suppliers not like the premium suppliers mentioned by others above.
Some arrive bent or with wobbles and its hard to prove it wasn't you. I have had 3 sets from different suppliers and all were bent on arrival.
So make sure you follow these steps after arrival.
1. Take photos while still in the opened shipping boxes and check for damage.
2. Dry fit one to the front and one to the rear to make sure they clear the caliper and suspension.
3. Spin each one on a tire balancer and observe any wobble or rim flat spots.
4. Then mount and balance tires.
Hope this helps
www.powerwheelspro.com supply some great replica rims and are high quality.
Be careful with replica suppliers not like the premium suppliers mentioned by others above.
Some arrive bent or with wobbles and its hard to prove it wasn't you. I have had 3 sets from different suppliers and all were bent on arrival.
So make sure you follow these steps after arrival.
1. Take photos while still in the opened shipping boxes and check for damage.
2. Dry fit one to the front and one to the rear to make sure they clear the caliper and suspension.
3. Spin each one on a tire balancer and observe any wobble or rim flat spots.
4. Then mount and balance tires.
Hope this helps
#14
Let's not forget to talk about how cheap Made in China wheels often carry fake JWL and VIA logos without actually being registered.
AND and TUV certification? Vs. certifcate of conformity? Forget it. No $100 rim is going to have it. Replicas being TUV certified? No freakin' chance.
I love my cheap isht from the Motherland, but these are a huge caveat emptor.
AND and TUV certification? Vs. certifcate of conformity? Forget it. No $100 rim is going to have it. Replicas being TUV certified? No freakin' chance.
I love my cheap isht from the Motherland, but these are a huge caveat emptor.
Last edited by TonyC; 12-20-2011 at 01:58 PM.
#15
MBWorld God!

Join Date: Jul 2010
Location: on my way
Posts: 30,655
Received 3,399 Likes
on
2,844 Posts
2012 CLS63
choices choices.......
don't be discouraged by seeing lots of other wheels in black......they look good!
and you have a Mercedes Benz, which looks even better.......
so don't trash the black idea quite yet
the Mandrus choice is a good way to go, inexpensive, made just for our cars, hubcentric, and they have several good styles to choose from.....
nah, I don't work there, LOL.......
but I do have a set......on my 550, they have been great, but I'm having my OEM's powder coated black just for something different for a while.....
I have Vossens on my amg which are freakin' nice......can't go wrong with those either.....that's all the working knowledge I have, but there are MANY choices.......too many in fact you know?
good luck
don't be discouraged by seeing lots of other wheels in black......they look good!
and you have a Mercedes Benz, which looks even better.......
so don't trash the black idea quite yet

the Mandrus choice is a good way to go, inexpensive, made just for our cars, hubcentric, and they have several good styles to choose from.....
nah, I don't work there, LOL.......
but I do have a set......on my 550, they have been great, but I'm having my OEM's powder coated black just for something different for a while.....
I have Vossens on my amg which are freakin' nice......can't go wrong with those either.....that's all the working knowledge I have, but there are MANY choices.......too many in fact you know?
good luck
#17
MBWorld Fanatic!
Does anyone make forged magnesium wheels for the AMG range?
The stock ones I had on my NSX were 17" staggered widths but weighed 14 lbs front and I think 15 lbs rear.
Anytime you get a Certified wheel weighing less than the diameter you have something desirable.
The stock ones I had on my NSX were 17" staggered widths but weighed 14 lbs front and I think 15 lbs rear.
Anytime you get a Certified wheel weighing less than the diameter you have something desirable.
#18
All I can say right now is we are working with a manufacturer that will introduce magnesium wheels - but they will be more expensive than aluminum wheels!
#19
Member
Join Date: Dec 2009
Location: Mercer Island, WA
Posts: 202
Likes: 0
Received 1 Like
on
1 Post
E500 "The Diplomat" W211

Have any of you heard of these companies? I just found them and cant find any reviews...
http://www.speedvisionmotorsport.com.../mercedes.html
Speed Vision Motorsports website linked to Euro Optionals.. maybe they are the same company?
http://www.eurooptionals.com/index.php/
Last edited by Freshly; 01-31-2012 at 01:58 AM. Reason: adding links
#20
Senior Member
Join Date: Aug 2011
Location: Atlanta, GA
Posts: 304
Likes: 0
Received 2 Likes
on
2 Posts
2007 E63 AMG, 1991 NSX, 2007 Corvette
If you are looking strictly at weight, check out the Morr wheel. Very sharp design and tons of research and development behind them.
Can't go wrong with HRE and Vossen.
Good Luck on your choice. There are many out there !!
I'll be making a choice soon and I'm not giving up on black as the color !!!
Can't go wrong with HRE and Vossen.
Good Luck on your choice. There are many out there !!
I'll be making a choice soon and I'm not giving up on black as the color !!!
#21
Junior Member
Join Date: Dec 2011
Posts: 62
Likes: 0
Received 0 Likes
on
0 Posts
06 E55, 10 Silverado LTZ 4x4